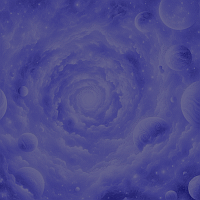
Use-Cases Automatisierung und Robotik
Prozessautomatisierung im Gesundheitswesen
Am Markt gibt es mittlerweile etablierte, spezialisierte Prozessautomatisierungslösungen für das Gesundheitswesen, die auf die Optimierung von Verwaltungs- und Abrechnungsprozessen sowie die Verbesserung des Datenzugriffs ausgerichtet sind. Auch werden verstärkt RPA-Plattformen genutzt, die speziell auf die Anforderungen des deutschen Gesundheitssektors zugeschnitten sind und intelligente Automatisierungslösungen für kritische Prozesse im Gesundheitswesen anbieten. Diese Systeme ermöglichen die Beschleunigung und Optimierung der Patientenaufnahme in Krankenhäusern. Mithilfe von RPA (Robotic Process Automation) und KI werden Aufnahmeprozesse automatisiert, was zu kürzeren Wartezeiten und einer effizienteren Ressourcennutzung führt. Die KI-gestützten Systeme übernehmen die Eingabe von Patientendaten in Aufnahmeformulare, überprüfen Identifikationen und Versicherungsinformationen sowie validieren diese mit hoher Genauigkeit. Gleichzeitig initiieren RPA-Bots automatisch Protokolle für Triage und Serviceplanung, überprüfen die Verfügbarkeit von Isolationsräumen und den Housekeeping-Status und benachrichtigen relevante Abteilungen wie Labor, Radiologie und Apotheke. Diese Automatisierung entlastet das medizinische Personal von zeitaufwändigen administrativen Aufgaben und ermöglicht es ihnen, sich verstärkt auf die direkte Patientenversorgung zu konzentrieren, was zu einer verbesserten Behandlungsqualität führt. Für den deutschen Markt sind zwei relevante Lösungen in diesem Bereich zu nennen.
Produktionsanlagen mit Hilfe digitaler Zwillinge rekonfigurieren
Bei BMW werden digitale Zwillinge eingesetzt, um das Layout der Produktionsanlagen bei der Einführung neuer Fahrzeugmodelle effizient zu rekonfigurieren. Fabrikplaner nutzen diese virtuellen Abbilder, um Maschinen und Roboter optimal in der Fabrik zu platzieren, bevor physische Änderungen vorgenommen werden. Durch den Einsatz dieser Technologie konnte BMW die Effizienz von Planungsprozessen um bis zu 30 Prozent steigern. Die digitalen Zwillinge ermöglichen es, verschiedene Szenarien zu simulieren und die Auswirkungen von Änderungen in Echtzeit zu analysieren, ohne den laufenden Betrieb zu beeinträchtigen. Dies führt zu einer verbesserten Produktionsplanung, reduzierten Ausfallzeiten und optimierten Prozessen. Für den deutschen Markt sind zwei relevante Lösungen in diesem Bereich zu nennen, die von mehreren Unternehmen eingesetzt werden: Zum einen die Digital-Twin-Plattform von Dassault Systèmes, die von BMW verwendet wird, und zum anderen die Omniverse-Plattform von Nvidia, die ebenfalls bei BMW zum Einsatz kommt. Diese Plattformen bieten umfassende Möglichkeiten zur Erstellung und Verwaltung digitaler Zwillinge in der Fertigungsindustrie und unterstützen Unternehmen dabei, ihre Produktionsprozesse zu digitalisieren und zu optimieren.
Autonome Drive Units
Im Lagermanagement hat sich der Einsatz von autonomen Drive Units mittlerweile etabliert. Diese selbstfahrenden Fahrzeuge nutzen KI, um sich effizient durch das Lager zu bewegen und Waren zu transportieren. Eine zentral gesteuerte künstliche Intelligenz berechnet für jedes Fahrzeug die optimale Route, basierend auf QR-Codes am Boden zur Orientierung. Dies ermöglicht einen kontinuierlichen Materialfluss, da die Drive Units rund um die Uhr eingesetzt werden können. Die KI-gesteuerten Fahrzeuge navigieren selbstständig durch verschiedene Lagerzonen, optimieren die Transportwege und beschleunigen so den gesamten Logistikprozess. Für den deutschen Markt sind zwei relevante Lösungen in diesem Bereich verfügbar: Zum einen bietet die ITM-predictive GmbH in Zusammenarbeit mit der Heidelberger Druckmaschinen AG eine KI-basierte Lösung zur Optimierung und Automatisierung lieferantengesteuerter Verbrauchslager an. Zum anderen entwickelt die Kardinal AI Technologien für die Logistikoptimierung, die auch im Bereich des Lagermanagements eingesetzt werden können.
Kollaborative Robots
Zur Optimierung von Demontage- und Recyclingprozessen für Batterien von E-Bikes und Elektrofahrzeugen werden kollaborative Roboter (Cobots) in Verbindung mit KI eingesetzt. In diesem Szenario arbeiten Menschen eng mit KI-gesteuerten Cobots zusammen, um die komplexe und potenziell gefährliche Aufgabe der Batteriedemontage durchzuführen. Die KI-Komponente ermöglicht es dem Cobot, die Gefühle und den Stresslevel des menschlichen Mitarbeiters zu erkennen und darauf zu reagieren, indem er beispielsweise seine Bewegungen und Arbeitsgeschwindigkeit anpasst. Dies führt zu einer sichereren und effizienteren Arbeitsumgebung, reduziert die physische und psychische Belastung der Mitarbeiter und optimiert gleichzeitig den Recyclingprozess. Für den deutschen Markt sind zwei relevante Lösungen in diesem Bereich verfügbar. Zum einen bietet Robco in Zusammenarbeit mit Robominds modulare Industrieroboter an, die mit der KI-basierten Robobrain-Technologie ausgestattet sind. Diese Lösung ermöglicht flexible Automatisierung für kleine und mittlere Unternehmen, insbesondere für Aufgaben wie Palettieren, Depalettieren und Bin-Picking. Zum anderen entwickelt Universal Robots Cobots, die in Deutschland zunehmend Anwendung finden. Diese Roboter können mit KI und maschinellem Lernen kombiniert werden, um Produktionsprozesse zu optimieren und die Zusammenarbeit zwischen Mensch und Maschine zu verbessern.
Autonome, mobile Roboter
Das Industrieunternehmen Fronius aus Neuhof-Dorfborn nutzt autonome, mobile Roboter in der Produktionsversorgung und im innerbetrieblichen Transport. Das Unternehmen setzt innovative Open Shuttle Fork Roboter ein, um Paletten autonom zu transportieren und die Produktionslinien flexibel mit Materialien zu versorgen. Diese AMR-Lösung ermöglicht es Fronius, selbstständig Änderungen im Materialfluss vorzunehmen und sowohl manuelle als auch automatisierte Aufträge in einem einzigen System zu verwalten. Dadurch werden die internen Prozesse optimiert, die Effizienz gesteigert und wertvolle Ressourcen für andere wichtige Aufgaben freigesetzt.
Überprüfung durch Roboter
In modernen Fertigungslinien in der Automobilindustrie werden KI-gesteuerte Roboter eingesetzt, um die Qualität von Karosserieteilen zu überprüfen. Diese Roboter sind mit hochauflösenden Kameras und Sensoren ausgestattet, die jedes einzelne Teil aus verschiedenen Winkeln scannen. Die KI-Software analysiert die Bilder in Echtzeit und vergleicht sie mit vordefinierten Qualitätsstandards. Sie erkennt selbst kleinste Abweichungen, wie Oberflächenunebenheiten, Farbunterschiede oder Materialfehler, die dem menschlichen Auge möglicherweise entgehen würden. Bei Entdeckung eines Defekts markiert das System das Teil automatisch zur weiteren Überprüfung oder Nachbearbeitung. Dieser Prozess erhöht nicht nur die Präzision der Qualitätskontrolle erheblich, sondern beschleunigt auch den gesamten Produktionsablauf. So hat die Firma Bosch Rexroth AG ein KI-basiertes Qualitätskontrollsystem namens „APAS inspector“ entwickelt, das in der Fertigungsindustrie eingesetzt wird. Es kombiniert Robotik und Bildverarbeitungstechnologie mit künstlicher Intelligenz, um Produktionsfehler frühzeitig zu erkennen, zu klassifizieren und diese Informationen an die Robotikeinheit weiterzuleiten.
Automatisierte Bauteilbearbeitung
Bei einem Spindelhubgetriebe-Hersteller werden zwei Roboter eingesetzt, um die Produktionslinien zu optimieren. Ein KI-gestützter Roboter belädt eine Fräsmaschine mit Rohteilen aus Metall und legt die fertigen Bauteile auf einem Nachbearbeitungsplatz ab. Dort übernimmt ein zweiter Roboter das Entgraten und Reinigen der Teile. Diese Automatisierung ermöglicht es dem Unternehmen, auch in mitarbeiterfreien Schichten nachts und am Wochenende zu produzieren, was zu einer erheblichen Steigerung der Produktivität und Wettbewerbsfähigkeit führt.
Zustandsüberwachung mit KI
Ein Use Case für den Einsatz von Automatisierung und Robotik in der KI zur Optimierung von Produktionslinien im Mittelstand ist die Implementierung von KI-gestützten Predictive-Maintenance-Systemen. Ein deutsches, mittelständisches Unternehmen im Maschinenbau sammelt beispielsweise Sensordaten aus Produktionsmaschinen und analysiert diese mithilfe von KI, um den Zustand der Maschinen in Echtzeit zu überwachen. Die KI erkennt Anomalien oder Verschleißmuster, die auf einen bevorstehenden Wartungsbedarf hinweisen. Dadurch können ungeplante Ausfälle vermieden, die Lebensdauer der Maschinen verlängert und Wartungskosten gesenkt werden. Zusätzlich kann die KI Produktionsprozesse optimieren, indem sie Engpässe identifiziert und Vorschläge für effizientere Abläufe macht. Dies führt zu einer höheren Produktivität, Kosteneinsparungen und einer verbesserten Wettbewerbsfähigkeit.
Bitte etwas Geduld
Hier wird der nächste Use-Case für Automatisierung und Robotik veröffentlicht.
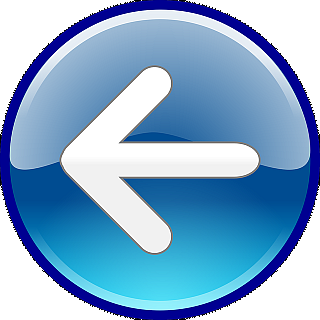